|
Audio
Consequence motor design:
A drive-unit (motor) for a loudspeaker
driver hast to fulfill a whole series of difficult tasks:
- It should generate the entire way to
work a possible linear driving force.
- It must be thermally resistant and derive
well the heat, which arises in the voice coil.
- It should be as compact as possible to
provide slightest reflection surface and to enable the integration
of a tweeter to the woofer
- The variable component (the voice coil)
should be as light as possible to reduce the inertia.
- It should be free of resonances
- It should have a high series of constance
and keep this for its whole life
- It should submit a possible low magnetic
field outwards
To fulfill all these requirements, only
one type of construction is applied by audio consequence:
The twin-neodymium-pot underhung
motor with voice coil made of aluminium wire (CCAW)
By using the same two incredibly
strong neodymium discs, which take the pole plate in
a pincer, an enormously strong and homogenous magnetic
field is generated. This is effectively screened out
by the surrounding steel jacket. At the same time the
massive jacket absorbs a big deal of heat energy and
release it to the environment and the aluminum-cast
basket.
In the tweeter the heat capacity
is increased by a machined aluminum body, which
is thermally coupled with the woofer motor. Audio
Consequence works with underhung engines, which means
that the voice coil itself is short, the air gap with
its magnetic field much more longer. Compared to conventional
overhang designs, the magnetic field can be shaped very
evenly, which reduces distortions, especially for low
frequencies and large strokes. Also, with this construction,
the entire drive can hold more heat, the system is thermally
stable and resilient. A weakness of such systems are
often relatively weak driving forces. Audio Consequences
succeded in this way by generating impressive 7.5 TM
wich means a very healty value for a driver in this
size and with a linear stroke of +/- 6.0 mm.
All voice coils are wound from
copper clad aluminum wire. This saves weight to the
voice coil, so it can be used where it also brings a
benefit - for the stability of the cones for example.
Wherever reasonable and necessary,
ventilation holes are also placed within the engines,
to avoid development of compression effects from the
beginning.
The electrical connection from
the voice coil to the connection terminal is not, as
usual, running on self-supporting and swinging leads,
but by symmetrically strands woven into the spider.
So it decreases the risk of broken strands substantially
and the possibility that the strand strikes during the
oscillation process to a different component is simply
excluded. The axisymmetric way of the strands is guaranteeing
a uniform load in the vibration axis.
|
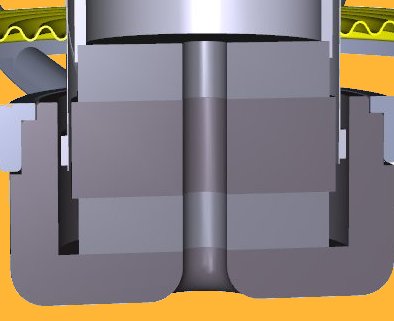
|
Finally, we thougt about the
connection terminals: The usual flat plug contacts
are useless in our view, in terms of quality of contact
and long-term stability. Although they allow solder
joints, by the ever more frequently used stronger supply
lines, this means increasing problems caused by heat
dissipation.
In our view the best and most
durable electrical connection is made through screw-down
terminals. They can get very strong cables, creating
a large contact area at high contact pressure and avoid
unnecessary material transitions, because no lugs, tubes
or plugs are needed. To be protected from corrosion
even after decades, the contact surfaces are gold plated.
|
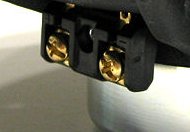
|
[back
to top]
Copyright(c) 2018 Audio Consequence. Alle Rechte vorbehalten.
|